Posts Tagged F-782D angles
F-782D Angles, Brake Reservoir, and Vent Lines Installed (2/9/13)
Posted by Ethan Jacoby in Construction, Forward Fuselage, Fuselage on February 9, 2013
5.0 Hours –
With most of the fabrication finished on the F-782D angles, it was time to drill them to the fuselage. It sounds simple, but it isn’t. The problem is that there are really no guides for the placement of these angles, there’s no way to clamp the angles to the fuselage, and you only drill through the F-7101 and not the side skin…drill too far, and you end up with some new holes that shouldn’t be in the outer skin! As usual, however, this turned out to be easier than I thought it would be.
In order to locate the correct position of the angles, I temporarily installed the F-782A cover plates. The position of plates determines the angle of the angles (wait…what?). Once the cover plates were installed, I simply used the edge of the plates to draw a line on the side of the fuselage that indicated the final angle and position of the plate. The F-782D angles are installed to match this line. To hold the angles in place while I drilled them, I used a short piece of double-sided tape and stuck them to the fuselage. This actually worked very well, except I had trouble removing the tape from the left side. Once stuck in place, I drilled the angles to the F-7101 gear web using a #30 drill with a drill stop placed slightly over 1/8″ from the tip.
After drilling the angles, I removed the double-sided tape and re-clecoed the angles to the fuselage. The cover plates were also re-positioned so I could mark the location of the fuel line cutout on the angles and check to make sure I would have enough edge distance on two screw holes I had to drill. Everything came off once again, and I cut the fuel line openings and drilled two #40 holes in the cover plates. Everything went back on, and I match-drilled the two new holes through to the angles and then enlarged the holes to #19 for #8 screws.
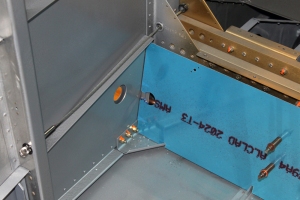
After drilling the F-782D angle to the fuselage, I positioned the F-782A cover to in order to determine how far inboard to drill holes for the screws.
Once final prep was finished on the angles, it was time to rivet them to the fuselage. The plans call for LP4-3 blind rivets. As many others have noted, these rivets are really too long for the application, but they can be installed by slowly pulling and pressing down. Instead, I opted to use some shorter rivets I had on hand from my fuel tank fix. The AD-42-H rivets I used have almost the same grip as the LP4-3 rivets, but, since they are closed end, they don’t have a shank extending past the end, adding to their overall length. With these rivets, installation was easy and all the rivet heads are sitting flush. After the angles were riveted t the fuselage, I had to rivet on the two platenuts. It would have been easier to rivet the platenuts first, but then I would have had access blocked to at least one blind rivet. Eventually, however, I managed to figure out how to get my squeezer to all of the platenut rivets.
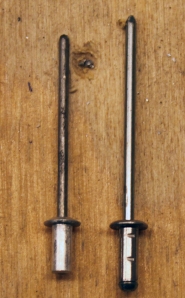
The plans called for LP4-3 (right) rivets to install the F-782D angles. However, they are way too long. Instead, I used AD-42-H (left) since they were the only rivets I had on hand that were a bit shorter.
Looking at my remaining parts, I decided to do something easy next…install the brake fluid reservoir. The reservoir is bolted to the upper right side of the firewall, using the upper firewall angle as a doubler. This was pretty much a matter of finding the correct position, drilling the bolt holes, and then figuring out where to drill a larger hole for where the reservoir passes through the firewall. Deburring the stainless steel firewall took more time than anything else. I also installed the firewall fittings for the brake lines. When I’m ready to install the actual brake lines, I’ll use some firewall sealant to seal up the gaps on the reservoir pass through.
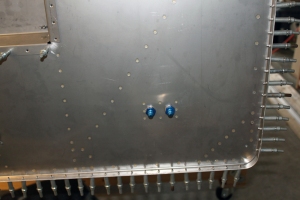
I installed the brake line fittings on the firewall. Eventually, these will connect the brake pedals to the lines that run to the wheels.
The last thing I did was to fabricate the cabin portion of the fuel vent lines. The vent lines supply positive pressure to the fuel tanks, and they have to be long in order to accommodate expansion of fuel in the tanks when the tanks are full. If expansion becomes too great, fuel will get dumped overboard. Some use a coiled length of tubing in the wing root, but I decided to stick to the plans and have the lines run into the cabin. Once the lines enter the fuselage from the wing, the travel up the forward fuselage bulkhead, then along the longeron, then back down the corner of the firewall/fuselage until they exit through the floor.
I started on the right side and it was a real pain to get all the curves formed. The initial curves are the toughest since the tubing has to make 4 small curves right after entering the fuselage. At this location, it has to curve to get around an angle, then curve the other way to stay clear of the rudder cable. Eventually, I had the tubing formed by using some, not so gentle, bending technique and clamping the tubing in position as I progressed. The left side went more quickly, and looks better than the right, but I’m OK with how they turned out.
Once the vent lines were bent, I installed the end fittings. My Rolo-Flair sure makes easy work of flaring the tube ends. I haven’t installed the lines on the fuselage yet, however, as I want to order the nicer fuel vents from JDair.com, rather than using the modified AN fittings as laid out in the plans. It will be easier to install everything at once so that I can adjust the fit as needed.
Flap Position Sensor Installed (2/8/13)
Posted by Ethan Jacoby in Center Fuselage, Construction, Forward Fuselage, Fuselage on February 8, 2013
3.0 Hours –
I finally received all the parts I needed to install the flap position sensor, so this became my main goal for the night. The sensor is the Ray Allen POS-12. It is just a box with a free-moving arm that can extend 1.2 inches. The movement of the arm gets converted to a signal that is sent to the avionics. My challenge is to link the sensor’s arm to the flaps in a way that full movement of the flaps is translated into 1.2 inches of travel on the sensor.
Not wanting to re-invent the wheel, I installed the sensor in a way that seems to be the most common among RV builders. The sensor itself is attached to the forward side of the back rest brace. The sensor is then connected to the flap weldment using a cushion clamp, some threaded rod and a couple of clevis ends.
First, I cut the threaded rod down to about 9 inches and then attached the clevis ends. Both the rods and the clevis ends I used were 4-40, and purchased from a local hobby shop’s aviation section (RC plane parts). One end attached directly to the sensor, and the other end was attached to the flap weldment using a bracket I made and a cushion clamp. The cushion clamp was positioned on the flap weldment arm that goes to motor about 1/2 inch forward of where arm meets the main cross member of the weldment. Once the clamp and sensor were attached to the weldment, I ran the flap motor until it was fully retracted. I then manually retracted the sensors arm and positioned the sensor on the back rest brace. With the position of the sensor set, I removed the back rest brace, drilled the sensor to the brace, and attached it with two #4 screws and stop nuts.
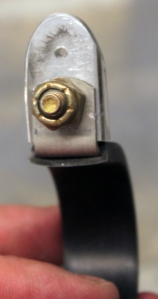
It still needs some finishing, but this is the backside of my bracket that will attach the position sensor’s pushrod to the flap weldment. This was a piece of angle, but one side was almost completely removed. Only enough is left to keep the bracket from rotating.
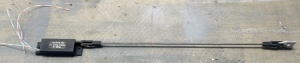
The complete flap position sensor setup. The clevis ends are RC parts from the local hobby shop, and they fit the sensor’s arm perfectly.
Once fully assembled, I ran the flap motor a couple of times to make sure the sensor could travel freely, and extend/retract fully. The first run wouldn’t allow the sensor to fully extend, so I had to re-position the cushion clamp further aft and shorten the pushrod slightly. After a little experimentation, I had everything dialed in.
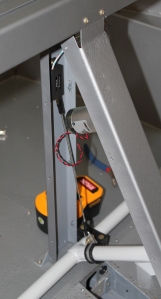
Flaps down, the sensor’s arm is retracted. The picture makes it look like the pushrod is right up against the flap motor, but it is really over an inch away.
Next, I started working on the F-782D angles. These angles are used to provide additional support to the F-782A cover plates that cover up some of the fuel/vent lines in the cockpit. The plans make the fabrication of these angles look more difficult than it actually was. In the end, it didn’t take long to do all the trimming and drilling.
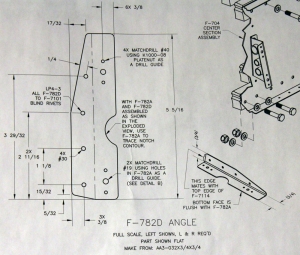
The F-782D brackets are fabricated from some .032″ x 3/4″ x 3/4″ angle. The plans make this part look more complicated than it is.
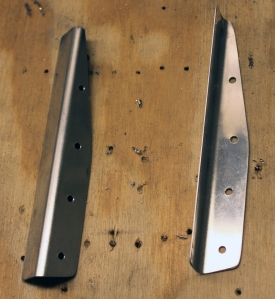
My F-782D angles after being trimmed and drilled for the holes that will attach the angles to the fuselage. The holes on the other side will get drilled in assembly with the F-782A cover plates.
In order to get an idea of the positioning of the angles, I temporarily installed the F-782A cover plates and marked where they butted up to the sides of the fuselage. Drilling the angles is going to be a bit of a challenge since access is limited and there is no way to clamp the angles to the fuselage. Instead, I’m going to try to use some double-sided tape to hold the angles in position while I start drilled. However, I decided to let this wait until tomorrow.