Archive for category Cowl
Tailwheel Installed And More Cowl Hinges (10/27/13)
Posted by Ethan Jacoby in Construction, Cowl, Finishing, Landing Gear on October 27, 2013
3.2 Hours –
When I went into the garage, I saw my tail wheel assembly sitting under my work bench, and I decided today would be a good day to install it on the fuselage. There was no rhyme or reason to doing this now…I just thought it would be cool to see 1/3 or the landing gear installed on the plane!
Installing the tailwheel was relatively easy. It slid into the mount with ease, and I had no problem lining up the bolt hole either. The only problem that arose was that the cut out on the bottom of the fuselage for access to the nut was slightly off-center from the nut itself. This made it difficult to get a socket on the nut. Not a problem though, I just ground down the edge of the socket until it could go through the access hole and seat on the nut. Once the nut was tightened, I stood back to admire the wheel, and I was happy to see that it was perfectly straight both vertically and horizontally.
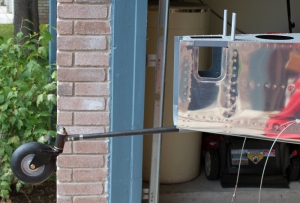
1/3 of the landing gear is installed! Unfortunately, this makes the fuselage so long that I have to push it back to get to my workbenches and pull it in to close the garage door.
Next, I reinstalled the engine mount in order to double-check that the gear legs would have enough clearance with the firewall. It only took a few minutes to get the engine mount reinstalled. The clearance for the left leg was good, but the right leg needed a little bit more material removed from the firewall. i was able to squeeze my Dremel plus sanding drum into the gear leg recess without removing the engine mount, and quickly removed any excess material.
I then turned my attention back to the hinges for the engine cowl. Again, I’m doing the hinges now, but hoping it doesn’t come back to bite me later. I don’t think there will be any problems when I go to fit the cowl, and it is easier to fit the hinges while removing the engine mount is simple (no main gear or engine installed). However, if there is a problem later on, drilling out a few rivets won’t be a big deal.
Today, I worked on the side hinges for the lower cowl. As with the lower hinges, I made shims from .020 aluminum strips, match-drilled the shims to the firewall and then match-drilled the hinges using the shims as a guide. Access to rivet the hinges was next to impossible with the engine mount installed, so the mount had to come back off. With the mount off, I could easily squeeze all rivets. I managed to finish the right hinge completely, but the left hinge still needs to be riveted.
Cowl Hinges Started (10/26/13)
Posted by Ethan Jacoby in Construction, Cowl, Finishing on October 26, 2013
1.5 Hours –
Today, I went back to work on the cowl hinges. I had already made the shims for the bottom hinges on the lower cowl, so I just needed to cut the actual hinges. This was pretty easy to do since I already had the shims drilled and could use them to cut the hinges to length and match drill them. Once the hinges were cut and drilled, I deburred, countersunk and dimpled the parts as needed, and then called it a day.
More Landing Gear Work (10/25/13)
Posted by Ethan Jacoby in Cowl, Finishing, Landing Gear on October 25, 2013
3.0 Hours –
One of the recommended bearing greases listed in the manual for the Matco wheel bearings is Aeroshell 22. Since this is a multipurpose grease that can be used for just about anything on the airframe, I decided to order some, and it will probably become the primary grease I use. Once the grease arrived, I watched a few videos on how to pack bearings, and then went into the garage to give it a go. The first bearing took me about a half hour, and I had grease everywhere! After changing gloves and loading my palm with another dollop of grease, the remaining bearings took just a couple of minutes each.
I also received some .020 shim stock from Onlinemetals.com. Onlinemetals.com will make custom cuts, so I ordered several strips of aluminum cut to 3 feet long and 0.5 inches wide. This width is perfect for shims, but the website lists a 1/8″ error margin on all cuts, so I also ordered a 1 foot by 2 foot sheet of aluminum that I could cut myself if needed. Fortunately, the strips were cut perfectly and should work well for shimming the cowl hinges.
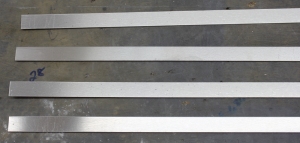
I bought some .020 shim stock from Onlinemetals.com. The best part is that they cut it into 1/2″ wide strips for me.
With the shim stock in hand, I cut two sections for shimming the lower edge of the bottom cowl. Once the shims were cut to length, I match drilled them to the firewall. At this point, instead of cutting and drilling the hinges, I decided to switch back to the landing gear. I did this mainly because the two main gear legs were taking up a lot of room on my workbench, and I just needed to do a couple of things to them before I could move them back down to the floor. The cowl hinges will have to wait!
I’m still a little confused about how the brakes are installed. The Matco brakes are a two-part assembly consisting of the brake caliper and a flange. The only aspect I am clear about is how the flange bolts to the gear leg. Once the flange is bolted on, the caliper can be installed. What is confusing me is that the caliper seems to “float” on the flange. It has two posts that slide into openings on the flange. There are no bolts that lock it into position, so I can only assume that the disc holds the caliper in place (once the wheel is installed). Still a little confused, I went ahead and installed the brake flanges on the main gear. Hopefully everything will become clear once I have the wheels and calipers in place.
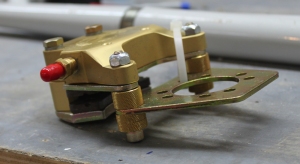
Another view of the brake assembly. The parts are zip-tied together because the caliper floats on the mounting flange. I’m struggling to visualize how this works…hopefully it will become clear once I have them on the wheels.
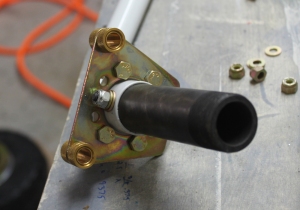
One of the brake flanges mounted on the main gear. The caliper posts slide into the large openings on the top and bottom.
Next, I made the six spacers that are needed for bolting the U-610 wheel pants brackets to the brake flanges/main gear legs. These are simple 13/32″ long sections of aluminum tube that act as standoffs for spacing the bracket from the brake disc.
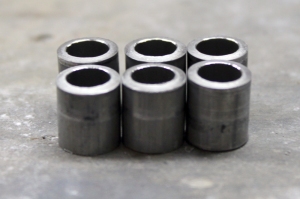
Several spacers had to be made for mounting the U-610 wheel pant brackets on the brake flanges. These spacers are each 13/32″ long.
Finally, I deburred and primed the U-610 wheel pants brackets. Along with the brackets, I also primed several parts for the canopy gas strut anchors since those had just been sitting on my workbench waiting for a larger batch of parts that needed to be primed.