Archive for category Horizontal Stabilizer
More Empennage Installation (4/19/14)
Posted by Ethan Jacoby in Aft Fuselage, Construction, Elevators, Empennage, Fuselage, Horizontal Stabilizer, Vertical Stabilizer on April 19, 2014
3.5 Hours –
Today, I continued working on the empennage installation. However, before I could do any more work on the plane, I had to gather all the parts. For the empennage, this meant climbing into the attic. Normally, this is an easy task, but with a garage full of large airplane parts, lowering the attic ladder isn’t always possible without significant rearrangement. Fortunately, I was able to push the tail of the fuselage far enough over for the ladder to come down. Then, it was just a matter of handing the tail pieces down to my wife one at a time. Surprisingly, these parts, which have been in the attic for years, had very little dust built-up on them, and absolutely no corrosion that I could see.
The first task was to install the elevators on the horizontal stabilizer and drill the elevator horns for the push rod bolt. To do this, the horizontal stabilizer was placed upside down on my workbench. The elevators were then installed with assembly pins and clamped in the “in-trail” position. The elevator horns are not a matched set, so there is a little variance between parts. Most builders do not have horns that are perfectly aligned. Although my horns were close, the right horn is about 1/4″ aft of the left horn. Once the aft horn is identified, it is drilled in the appropriate location with a #30 pilot hole. Then, I made a spacer/drill guide for between the horns using a block of wood. This spacer has a #30 hole drilled through it using the drill press to ensure that the hole is perpendicular to the block. The spacer is then inserted between the horns and used to guide the drill for cutting the hole in the opposite elevator horn. Once both horns have a pilot hole, the holes are enlarged for an AN3 bolt.
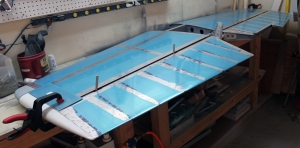
On the workbench, the elevators are temporarily installed on the horizontal stabilizer and clamped in the “in-trail” position.
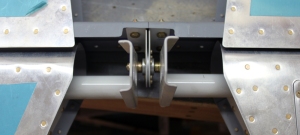
The elevator horns aren’t a matched set, so one is usually aft of the other, and this must be accounted for when drilling the hole where the push-rod will attach. My right elevator horn is slightly aft (left in this picture since the whole assembly is upside down).
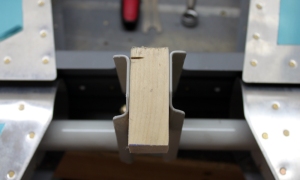
A wood block is used to make sure that the holes in the elevator horns are perfectly aligned. The wood block has a #30 hole through it that was made with the drill press to ensure straightness.
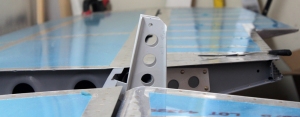
The aft (right) horn is drilled to #30 first. Then the block is used to align the drill for forward (left) horn. Once the pilot holes are drilled, the block is removed and the holes are enlarged for an AN3 bolt.
Next, the elevators were removed from the horizontal stabilizer so I could move the parts to the fuselage. Once the horizontal stabilizer was on the fuselage, the elevators were reattached, and I was able to bolt the push rod to both elevators. With the push rod attached, I checked to make sure the elevators were aligned with each other and moved freely in both directions. With the lightest touch, I could easily move the elevators, and there was no binding of any kind. Needless to say, I had to play with elevators for a few minutes!
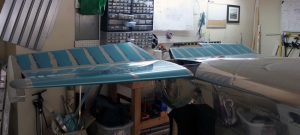
Once the elevator horns were drilled, the whole assembly was installed on the fuselage and the elevators were connect to the pushrod. Here they are, moving together, in the up position.
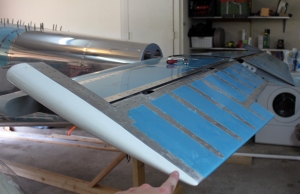
And, of course, here they are in the down position. Ignore my finger…without holding them, they want to go back to neutral or up.
Once I finished playing with the elevators, I moved on to the vertical stabilizer. The first thing is to cut 5/8″ from the bottom of the forward spar of the vertical stabilizer. I’m not sure why Van’s doesn’t have you do this before assembling the vertical stabilizer since it would be easier at that time, but it was still relatively easy to do this using my Dremel and cut-off disc. Next, I clamped the F-781 attach plate to the forward spar of the horizontal stabilizer and then clamped the vertical stabilizer to the fuselage. At this point, the vertical stabilizer has to be positioned so that it is exactly vertical and the leading edge is 1/4″ left of center (to offset left turning tendency). I took some measurements and re-positioned the vertical stabilizer to where I think the fit is correct, but I want to take a break and re-measure before doing any actual drilling. I’ll return to this tomorrow.
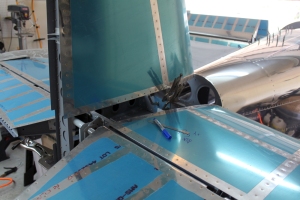
The vertical stabilizer is clamped to the horizontal stabilizer’s forward spar and to the rear bulkhead of the fuselage.
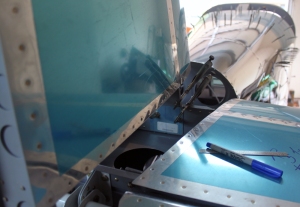
A closer view of how the vertical stabilizer is clamped to the horizontal stabilizer’s forward spar.
In the meantime, I started fabricating the F-712D up elevator stop. This part is fashioned from some stock angle, and I managed to get the rough cuts done, but it still needs a lot of finishing work. However, since this is the first part to get drilled to the vertical stabilizer, it will be at the top of my priority list.
Horizontal Stabilizer Installation Continued (4/16/14)
Posted by Ethan Jacoby in Aft Fuselage, Construction, Empennage, Fuselage, Horizontal Stabilizer on April 16, 2014
1.0 Hours –
The goal for the day was to finish attaching the horizontal stabilizer to the fuselage. Since only four holes needed to be drilled, this should have been an easy task…and it was.
First, I had to take a few measurements to insure that the horizontal stabilizer’s incidence was at 0°. With the 3/16″ spacers under the aft spar, the incidence should be set, but the distance from the aft deck to the tooling holes in the inboard ribs of the horizontal stabilizer ribs can be used to confirm the incidence. There are several tooling holes, and the distance was equal on all of them. Therefore, 0° incidence.
With the incidence set, it was just a matter of drilling four holes through the F-711C vertical bars and aft spar of the horizontal stabilizer. Nothing complicated here. Access was easy, and there is a ton of material in this area, making edge distance concerns negligible. I drilled the holes to #30, then to #19, before finally reaming them to the appropriate diameter for the AN3 bolts.
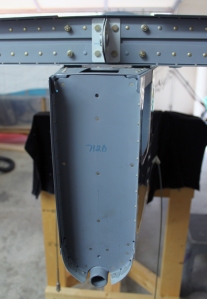
The holes for the four bolts that attach the horizontal stabilizer to the F-711C vertical bars were easy to drill.
Of course, as soon as the horizontal stabilizer was installed on the fuselage, it had to come back off. There were two reasons for this. The first is that I need to fit the elevators and drill the elevator horns for attaching the push rod. Second, the elevators, and all of the other empennage parts have been stored in our attic, and, with the horizontal stabilizer attached to the fuselage, there just isn’t enough room in the garage to gain access to the attic.
Horizontal Stabilizer Installation Started (4/14/14)
Posted by Ethan Jacoby in Aft Fuselage, Construction, Empennage, Fuselage, Horizontal Stabilizer on April 14, 2014
2.5 Hours –
My plan for the airplane is to finish up some of the little things now. Then, when the weather gets hot, I want to finish up the canopy. The next thing on my list of “little things” is to install the tail feathers.
First things first, I decided to turn the fuselage around so that I would have more room to work on the tail without having to move the plane halfway out of the garage anytime I wanted to do something. Although turning the fuselage around should be an easy task, my current garage setup made it a little more challenging. Our kayaks, lawnmower, and a few other things had to be moved out of the garage so I would have enough room to back the fuselage out. Once the path was clear, backing the fuselage out, turning it around on the driveway, and pushing it back in was a pretty easy task thanks to my rolling fuselage cart that has four castering wheels instead of just two.
Once the fuselage (and all the other stuff) was back in the garage, I pulled the horizontal stabilizer down off the wall for the first time in about 4 years. After wiping off some of the dust, I gave the horizontal stabilizer a thorough inspection. Since this is the first part of the plane that gets built, I somewhat expected to find some sub-par craftsmanship. However, I didn’t find anything that I wouldn’t consider passable today. So, on the fuselage it went.
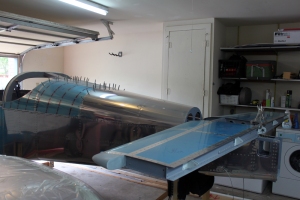
The first thing I had to do was turn the fuselage around in the garage so I would have more room to work on the tail. Then, the horizontal stabilizer came off the wall for the first time in 4 years.
To position the horizontal stabilizer, I placed all of the spacers and shims where they needed to go (3/16″ drill bits used as spacers on the aft spar), and then clamped the aft spar to the F-711C vertical bars. Then, I measured from a point on each side of the fuselage to one of the aft, outer rivets on each side of the stabilizer. If the measurements are equal, the stabilizer is centered. Of course, it took multiple measurements and multiple tiny movements to get the stabilizer’s position just right. Once positioned, I made sure everything was solidly clamped, then marked out the locations for drilling the forward horizontal stabilizer spar to the fuselage.
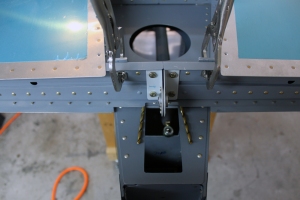
The aft spar needs to sit 3/16″ above the deck in order to getting the necessary 0 degrees of incidence. As Van’s recommends, I used two 3/16″ drill bits as spacers.
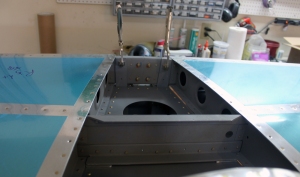
Clamping the aft spar was easy, but the forward spar was more challenging due to limited access. Once clamped, there was a lot of measuring, moving, re-measuring, moving…before finally drilling.
Normally, drilling four holes is a pretty simple task. However, the four holes that will be used to attached the horizontal stabilizer’s forward spar to the fuselage are critical holes, and half of the assembly is under the aft deck and very hard to visualize. In addition, the two out holes also go through the longerons, where edge distance is once again critical, but the part is hidden from view. After a lot of careful measurements, I decided to go for it and drilled the first hole. Edge distance was ok, so on to the next, then the next and the last. All four holes are now drilled and edge distance is acceptable all around.
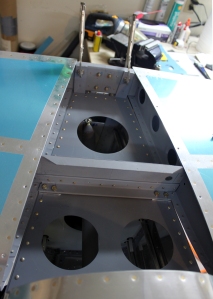
This is the best picture of the many bad pictures I took of the forward spar after drilling. All four holes have good edge distance underneath.
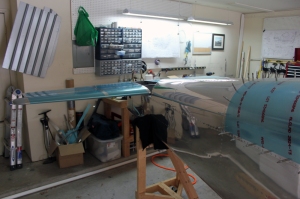
Another view of the horizontal stabilizer, which now has the forward spar drilled and bolted to the fuselage. Next, the four holes in the aft spar have to be drilled, but those are easy compared to the forward holes.
Next, the aft spar of the horizontal stabilizer needs to be drilled to the F-711C vertical bars. Fortunately, these everything is visible and easy to access and there is plenty of bulk in the area, making edge distance a non-factor. However, I decided to call it a day.
Horizontal Stabilizer Tips Finished and Riveted (5/13/10)
Posted by Ethan Jacoby in Construction, Empennage, Horizontal Stabilizer on May 13, 2010
0.5 Hours –
After doing bits of work here and there on the HS tips, they are finally finished for the second time! This time, I made sure to check the fit with the elevators after each step. The pictures don’t really do them justice. The flash makes the aft surface look uneven, but it is really just an effect of sand the surface smooth. When sanding, primer is knocked off high spots, leaving the white micro to show through more than it does on the low spots.
Redoing The HS Tips (5/9/10)
Posted by Ethan Jacoby in Construction, Empennage, Horizontal Stabilizer on May 7, 2010
1.0 Hours –
Despite my lack of posts over the last week and a half, I’ve actually been working on the plane almost every day. However, as I’ve stated before, with fiberglass, it is 15 minutes of work followed by hours of drying time.
On my last post, I had just finished filling and priming the HS tips. They looked beautiful too. Unfortunately (or fortunately), I checked the fit one last time before riveting them on. To be sure the fit was OK, I also attached the elevators to make sure they had enough clearance. Well, they didn’t! The elevators could no longer swing because I built up the aft surface of the HS tips too much. Come on…I only had two layers of micro, two layers of thinned epoxy on top of that, and two layers of filler primer on top of that!!! The prime culprit really was the micro. I had the tips cut down to the perfect length, then filled past that with micro.
So, my once beautiful HS tips had to be sanded all the way back down to the wood rib, leaving just a bit of micro in the low spots, then re-sealed and re-primed. Now, they look just as good as before, but still have the necessary clearance for the elevators to swing. At least I’m still waiting for my wings and have plenty of time to play with these tips!
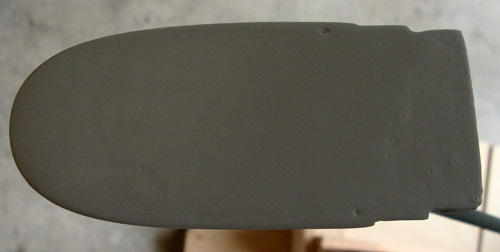
Pinholes in the micro become obvious once primer is applied. Sand, seal, prime, repeat until the holes are gone.
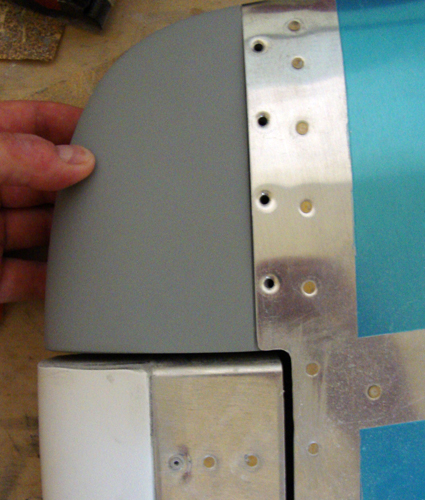
The picture makes the gap look bigger than it is. Too much micro, and the gap dissappears (ask me how I know).
In addition, I bought and assembled a new BBQ grill this weekend. Assembly took about 2 hours. If Van’s wrote the instruction manual, assembly probably would have taken an hour max!
Primed Horizontal Stabilizer Tips (4/28/10)
Posted by Ethan Jacoby in Construction, Empennage, Horizontal Stabilizer on April 28, 2010
0.5 Hours –
This evening, I spent a few minutes countersinking the HS tips and dimpling the HS skin. Once this was done, I cleaned the HS tips with soap and water and then sprayed on two coats of primer. It looks like I may still have some pinholes to deal with on the aft surface of the tips. Once the primer is dry, and if pinholes are present, I will probably sand the primer and then add another layer of epoxy to try to seal these holes.
Still Working On The VS and HS Tips (4/23/10)
Posted by Ethan Jacoby in Construction, Empennage, Horizontal Stabilizer, Vertical Stabilizer on April 23, 2010
0.7 Hours –
Today, I was able to get another 45 minutes of work in on the HS and VS tips. As usual, now they have to set overnight before I can do anything else.
After sanding down the layer of micro on the aft surface of the HS tips, there were a lot of pinholes present. On the VS tip, I decided to layer on some more micro, but, this time, I decided just to put on two coats of straight epoxy and see if that seals the holes.
Once my epoxy was on the HS tips, I turned my attention back to the VS tip. I had piled on some micro to see if I could fill the gap on the forward edge between the fiberglass tip and the metal skin. I did a quick, rough sand on this micro, and it looks like the gap is nicely filled. I still need to do a bit more sanding, follow the sanding with a coat of primer, and the gap should be a distant memory!
More Work On The Horizontal Stabilizer Tips (4/21/10)
Posted by Ethan Jacoby in Construction, Empennage, Horizontal Stabilizer, Vertical Stabilizer on April 21, 2010
0.8 Hours –
Since this is more fiberglass work, as with the last few posts, this entry covers work that occurred over multiple days. I’m combining some of these because I can’t justify writing one post for something that took 15 minutes to do and then had to set overnight before I could do more work.
The other night, I reinforced my wood HS tip ribs by adding a layer of fiberglass to the inside of the joint over the flox filet. Once the epoxy was set, I returned to the tips today and put a layer of micro over the aft face of the wood ribs. This was done in the same manner as with the vertical stabilizer tip. However, I tried to make the micro a bit thicker in order to prevent it from running down the side of the tips (it took a lot of sanding to fix that on the VS tip). This time, my micro was the consistency of thick frosting rather than a runny glaze. This thicker micro had to be spread on instead of poured, and it seems to have fewer air bubbles than my previous, runnier micro.
Once I coated both HS tip ribs, I still had some micro left over. With the extra, I decided to slather some on the gap that is present on the leading edge of the vertical stabilizer where the aluminum and tip meet. I’m hoping the micro will fill the gap and be easy to sand back to the contour of the vertical stabilizer. If it doesn’t work, I may have to glass the seam on the VS and I’m trying to avoid this.
Horizontal Stabilizer Tip Rib Work (4/18/10)
Posted by Ethan Jacoby in Construction, Empennage, Horizontal Stabilizer on April 19, 2010
1.0 Hours –
Today, I was able to fit the left HS tip, construct the wood rib for it, and bond both the ribs to both tips. This time, I decided to bond the ribs in place while the tips were clecoed on the HS. Since the tips deform quite a bit when not clecoed in place, I was worried that the fit may not be quite right if I removed the tips and bonded the ribs outside the HS. Once the flox set, I removed the tips and laid a fillet of flox around the inside joint of each tip/rib combo. Tomorrow, I’ll reinforce them with some glass.
On a more positive note, about one more month until my wings arrive. Hopefully, when it comes time to order the fuselage, I’ll be able to save the money earlier and not have a construction gap after the wings are completed.
Started Right Horizontal Stabilizer Tip (4/16/10)
Posted by Ethan Jacoby in Construction, Empennage, Horizontal Stabilizer on April 17, 2010
1.0 Hours –
The HS tips require the most work of all the empennage tips. Since some metal is cut from the end of the stabilizer to accommodate the elevators, an equal amount of the HS tip also has to be removed. In addition, the horizontal stabilizer is not pre-punched for the tip attachment locations. This is the only part of the empennage where an entire row of rivet holes is missing. Like the VS tip, the HS tips are also open ended and I will need to make some wood ribs to close them off.
I started by trimming the tip. Using my Dremel, I cut about 0.2” from the flange, and removed over an inch from the aft end to allow the elevator to swing. Being cautious, I made sure to remove less than required from the aft end. It’s much easier to sand it down the rest of the way than to rebuild it with fiberglass.
Next, I needed to measure and mark the horizontal stabilizer for the tip attachment holes. Since the flange on the tip is 0.5” wide, I decided that my rivet holes should be 0.25” from the edge of the HS. Drawing this line was the easy part. Now, how do I decide on the number of rivets to use to attach the tip and how far apart do they need to be spaced?

Unlike the other empennage components, the horizontal stabilizer is not prepunched for the tips. Here, I measured for drilling.
After looking at the other empennage tips (all of which have different rivet spacing), I decided to place the first rivet 1” from the leading edge and then place three more rivets at 1.25” intervals for a total of four rivets per side. Once I marked this pattern, I used a center punch and then drilled the holes to #40.
Another difficulty with the HS tips is that they are not quite wide enough. If I clamp one side to the HS, the other side is almost a half inch from the flange. However, they do easily stretch to fit the HS. With this in mind, I clamped both sides of the tip in place and started match drilling the tip to the holes I had just made in the HS. As with the other tips, I drilled my first hole, then carefully re-checked the fit before moving on to the next hole.
Once all the holes were drilled and the tip was clecoed on, I attached the elevator to check how much more of the tip would need to be removed. Fortunately, not much! The aft end of the tip will require a bit more sanding in order to make a nice, even gap the entire length. The elevator tip also sticks out a bit more than the HS tip. To fix this, I’ll probably put a layer of micro on and then sand it to shape so that it is even with the elevator’s tip. On one builder’s site, I saw that they actually closed the entire HS/elevator tip gap with micro, sand the final shape, then re-cut the gap with a saw. I may try this as well.